Digitalising construction safety
The construction industry needs to increase its safety standards by enhancing contractor performance and worker competency, and embedding a culture of shared ownership, including those in the supply chain and subcontractors.
Many contractors were seen to operate below acceptable safety standards in the earlier phases of Malaysia’s mega infrastructure projects due to limited understanding of hazards and training for high-risk activities, says Adil Putra Ahmad, project director at SRS LRT Sdn Bhd, a subsidiary of Gamuda Bhd.
“Historical site incidents have highlighted the critical need to re-evaluate safety practices and raise safety standards across the industry, which is why Gamuda amplifies its digital implementation to enhance safety protocols at construction sites. This is crucial in an industry that is traditionally associated with paper-based processes and manual oversight.”
Gamuda has been implementing digitalisation at every stage of its developments, including project-specific training, competency, machinery, carrot-and-stick approach and safety audits, while enabling predictive risk management and data-driven decision-making by leveraging a single data warehouse system, says Adil.
The regional engineering and construction company has continuously integrated advanced technologies into all of its projects, including the Klang Valley Mass Rapid Transit (KVMRT) Kajang and Putrajaya lines, Sydney Metro West, Singapore’s Defu station and tunnels, and the upcoming Penang light rail transit (LRT) Mutiara Line.
The company uses data-driven project management to enhance efficiency and accountability, namely the Gamuda Digital Operating System (GDOS) and Autodesk Construction Cloud (ACC), to consolidate all project data into a unified cloud-based ecosystem. “Information silos and geographical barriers are eliminated. When safety data, progress tracking and resource management are all in one system, smarter decisions can be made accurately and faster,” Adil explains.
Protecting workers and the public
Worker certification is a mandatory requirement for ensuring on-site safety at Gamuda’s construction sites. All workers are required to complete structured training at dedicated training centres before being allowed to gain access to work sites and operate machinery, says Adil.
To smooth the process, the company has digitalised its training and certification modules. Digital assessments are now conducted on tablets, which have replaced traditional paper-based exams and rigid time settings.
“The interactive tests are mainly in English, Bahasa Malaysia and Chinese, and have now been expanded to the languages used in Indonesia, Bangladesh, Pakistan, Nepal, Myanmar and Vietnam — to effectively assess the skills of the diverse local and foreign workforce,” he says.
Successful candidates are issued blue, grey or black certification cards. Each card is embedded with a unique QR code, which serves as a digital passport for site access.
The blue card is mandatory for all project personnel, which ensures competency in project SHE protocols.
Personnel with valid Construction Industry Development Board (CIDB) green cards can obtain their blue card by completing the required basic health and safety induction training.
The grey card is issued to personnel involved in high-risk activities such as lifting and hoisting, scaffolding, temporary works, plant and machinery operation, launching as well as electrical safety.
Meanwhile, the black card is for supervisors, managers and senior management.
Essentially, the QR code enables secure access and ensures worker registration. That is because workers’ facial data, certification status and other relevant details are embedded in the respective QR code.
With this, all Gamuda construction sites are equipped with access control systems (ACS) that use advanced facial recognition technology. Only workers who pass through these ACS gates are allowed to attend the daily pre-task talks before commencing their duties.
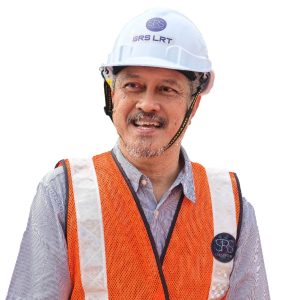
“Construction will always involve certain risks but with these digital tools, we are now able to predict and prevent issues before they become problems. — Adil Putra Ahmad, project director at SRS LRT Sdn Bhd”
“Thereafter, safety and health officers may conduct ad hoc checks on workers’ validity with a simple scan of their QR code anytime and anywhere,” says Adil.
“Another key safety feature introduced is the certification of all equipment and machinery on-site. Following a thorough inspection, each machine is assigned a QR code, which serves as a quick reference to confirm it meets safety standards and is safe for use, thereby enhancing overall site safety,” he explains.
The QR code is generated via digital forms on the ACC platform. “Any machinery or temporary structure that fails inspection is immediately flagged for rectification or removal from the site. QR tagging allows for fast and accurate verification to maintain consistent safety oversight throughout the construction process,” says Adil.
Carrot-and-stick approach to subcontractor safety
That is not all. Gamuda implements a comprehensive incentive and compliance system across all its construction sites, which is designed to meet the highest safety standards while promoting high performance.
Contractors and subcontractors who demonstrate outstanding safety practices will receive incentives, which create a positive culture that values safety, says Adil.
“Deviation from safety practices and compliance standards would trigger a structured escalation of corrective measures, ranging from initial observations to non-compliance reports, stop-work orders and financial repercussions when necessary. This dual approach ensures that safety remains non-negotiable across all Gamuda projects,” he stresses.
Having a lasting impact
Ultimately, Gamuda expects its digitalisation efforts to have a wide range of benefits. For example, there would be increased workforce confidence and strengthened contractor safety accountability, says Adil.
To add to this, digitalisation also connects Gamuda with its stakeholders such as the residents, the authorities and the public, allowing for easy communication and information-sharing, which enables the speeding up of resolution if any issues were to arise, he adds.
Such efforts have allowed Gamuda to have zero incidents involving the public in its past projects and to see a 75% reduction in lost time due to injuries in the KVMRT project compared with earlier phases and industry benchmarks, says Adil.
“We have trained over 20,500 workers for safety passports, while all our subcontractors have recorded 100% compliance with the mandatory safety induction and training programmes.”
Safety is our responsibility
Adil says Gamuda’s digital innovations in urban construction has directly benefited the public through enhanced public safety, shorter construction timelines, reduced traffic disruptions and maximum transparency through digital process tracking.
By prioritising digital construction, the company has shown its commitment to public comfort, mobility and quality of life — principles that will continue to guide its projects, including the Penang Mutiara Line, he adds.
“Construction will always involve certain risks but with these digital tools, we are now able to predict and prevent issues before they become problems. That’s not just good business — it’s our responsibility to our workers and the communities we build in.”